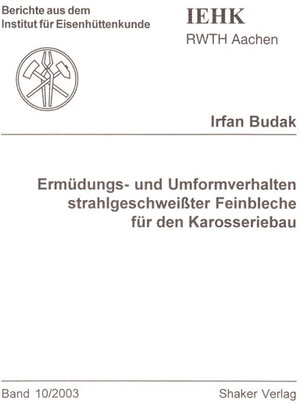
×
Ermüdungs- und Umformverhalten strahlgeschweißter Feinbleche für den Karosseriebau
von Irfan BudakTailored Blanks are a light weight structure concept for car bodies. It had been first mentioned in the eighties and their application has expanded in recent time. In this concept, several steel qualities or several thicknesses are joined together. The joined blanks are contoured suitable to components which will be produced. Using this method, several conditions or requirements can be performed on several segments of components and a weight reduction with better properties can be reached simultaneously.
The aim of this study is to determine the limits that occur due to the material and the welding process and to point out the possibilities for expansion of Tailored Blanks regarding thickness and material combination and welding technology. For this purpose, it is necessary to investigate the weldability of innovative high strength steels such as DP- and TRIP-steels and to determine the influencing parameters on the mechanical properties.
The investigated materials (ZStE340, DC04, IF-, TRIP- and DP-steels) have a wide spectrum of chemical and mechanical properties. Therefore the results of this investigation can be, in many aspects, generalised for other steel qualities.
Typical for laser beam welding is a narrow weld seam, a low heat input and a high welding speed. A high process stability and a low number of process parameters are the main advantages for the production of Tailored Blanks. The disadvantage of this process is a very strong requirement for the preparation of the cutted edges.
Laser beam welding with additional wire and electron beam welding has been investigated as an alternative processes to laser beam welding. According to practicablity and process stability, the electron beam welding is similar to laser beam welding. The weld seam at electron beam welding is normally larger in width. At laser beam welding additional attention must be paid for positioning additional wires and for matching the wire speed to the welding speed. Therefore there are more parameters to set.
Strength, formability and fatigue behaviour of welded blanks have been investigated subsequent to the investigation of the weldability of steel grades.
In order to quantify the influence of welding on the mechanical properties, the terms “metallurgical or geometrical notch effect” has been used.
The metallurgical notch effect occurs due to the changes on microstructure and chemical composition, in the heat affected zone and in the weld seam. It can be quantified through the hardness increase in these zones. The geometrical notch effect occurs due to the geometrical discontinuities at the weld seam. It will be quantified through a stress concentration factor.
In order to support the interpretation of results of the mechanical tests, metallographic investigations, hardness measurement and line scan analysis have been performed.
An important part of this study was the investigation of fatigue behaviour of welded blanks. Measurements to reduce the influences of metallurgical and geometrical notch effects on the fatigue behaviour have been suggested.
The most important results can be summarised as follow:
Summarising all of the investigated materials and weld processes have shown a selective suitability for several aims. For example, the narrow weld seam at laser beam welding is advantageous for the forming behaviour, while the sharp geometrical and metallurgical notch effect at the weld seam is disadvantageous for the fatigue behaviour. The geometrical notch effect and the hardess increase at the weld seam can be reduced by using electron beam welding. But electron beam welded blanks have poorly forming behaviour because of the wide weld seam. The expense of edge preparation can be reduced by laser beam welding with additional wire. But because of low strength and formability, these blanks could only be used for components with average requirements. Therefore, the selection of material and weld process will proceed depending on application requirements and cost factor.
The aim of this study is to determine the limits that occur due to the material and the welding process and to point out the possibilities for expansion of Tailored Blanks regarding thickness and material combination and welding technology. For this purpose, it is necessary to investigate the weldability of innovative high strength steels such as DP- and TRIP-steels and to determine the influencing parameters on the mechanical properties.
The investigated materials (ZStE340, DC04, IF-, TRIP- and DP-steels) have a wide spectrum of chemical and mechanical properties. Therefore the results of this investigation can be, in many aspects, generalised for other steel qualities.
Typical for laser beam welding is a narrow weld seam, a low heat input and a high welding speed. A high process stability and a low number of process parameters are the main advantages for the production of Tailored Blanks. The disadvantage of this process is a very strong requirement for the preparation of the cutted edges.
Laser beam welding with additional wire and electron beam welding has been investigated as an alternative processes to laser beam welding. According to practicablity and process stability, the electron beam welding is similar to laser beam welding. The weld seam at electron beam welding is normally larger in width. At laser beam welding additional attention must be paid for positioning additional wires and for matching the wire speed to the welding speed. Therefore there are more parameters to set.
Strength, formability and fatigue behaviour of welded blanks have been investigated subsequent to the investigation of the weldability of steel grades.
In order to quantify the influence of welding on the mechanical properties, the terms “metallurgical or geometrical notch effect” has been used.
The metallurgical notch effect occurs due to the changes on microstructure and chemical composition, in the heat affected zone and in the weld seam. It can be quantified through the hardness increase in these zones. The geometrical notch effect occurs due to the geometrical discontinuities at the weld seam. It will be quantified through a stress concentration factor.
In order to support the interpretation of results of the mechanical tests, metallographic investigations, hardness measurement and line scan analysis have been performed.
An important part of this study was the investigation of fatigue behaviour of welded blanks. Measurements to reduce the influences of metallurgical and geometrical notch effects on the fatigue behaviour have been suggested.
The most important results can be summarised as follow:
- The metallurgical notch effect can not be eliminated through additional wire because of the hardening occurring in the heat affected zone.
- Pre-forming and following heat treatment at the paint baking temperature lead to a decrease of the metallurgical notch effect.
- The metallurgical notch effect can be reduced when defocusing the laser beam.
- The geometrical and metallurgical notch effects must be taken into consideration together. For example: If the geometrical notch effect can be eliminated completely during mechanical treatment, the metallurgical notch effect has no influence on fatigue behaviour anymore.
Summarising all of the investigated materials and weld processes have shown a selective suitability for several aims. For example, the narrow weld seam at laser beam welding is advantageous for the forming behaviour, while the sharp geometrical and metallurgical notch effect at the weld seam is disadvantageous for the fatigue behaviour. The geometrical notch effect and the hardess increase at the weld seam can be reduced by using electron beam welding. But electron beam welded blanks have poorly forming behaviour because of the wide weld seam. The expense of edge preparation can be reduced by laser beam welding with additional wire. But because of low strength and formability, these blanks could only be used for components with average requirements. Therefore, the selection of material and weld process will proceed depending on application requirements and cost factor.