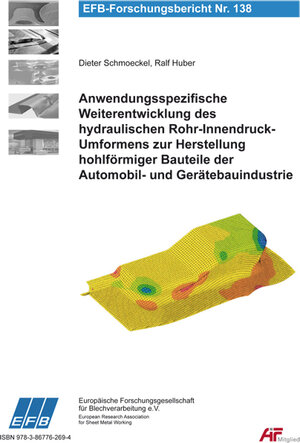
×
Anwendungsspezifische Weiterentwicklung des hydraulischen Rohr-Innendruck-Umformens zur Herstellung hohlförmiger Bauteile der Automobil- und Gerätebauindustrie
von Dieter Schmoeckel und Ralf HuberIm Rahmen dieses Forschungsvorhabens wurden für das Innenhochdruck-Umformen von unverschweißten Blechen die Verfahrensgrundlagen Zuführung des Umformmediums zwischen die Blechplatinen, Abdichtung der Blechplatinen im Flansch gegen den lnnendruck, Konturausformen mittels Innendruck und Schneiden mit Innendruck untersucht sowie der Einsatz der Druckfügetechnik im Umformwerkzeug erprobt. Das Werkstückstoffspektrum umfaßte die gängigen Feinblechgüten im Automobil- und Gerätebau DC04, AIMgG5Mn, ZStE340 und X5CrNi18 9 im Wandstärkenbereich 1 mm bzw. 1.15mm.
Die untersuchten Andocksysteme, also die Art der Zuführung des Umformmediums zwischen die Blechplatinen, lassen sich prinzipiell in Andocksysteme innerhalb und außerhalb der Blechtrennebene einteilen. Bei den Andocksystemen außerhalb der Blechtrennebene kann noch unterschieden werden, ob das Andocksystem im Flansch oder in der Aufweitzone liegt. Die durchgeführten Untersuchungen zeigten, daß jedes Andocksystem mit spezifischen Vor- und Nachteilen behaftet ist, die bei unterschiedlichen Bauteilgeometrien unterschiedlich zum Tragen kommen können.
Die Auswahl eines Andocksystems für ein Bauteil hat demnach immer bauteilspezifisch zu erfolgen. Die im Rahmen dieses Forschungsvorhabens betrachtete Abdichtung der Blechplatinen gegen das Umformmedium im Flansch hatte zum Ziel alleine über eine ausreichende Flächenpressung zwischen den Blechen, welche über die Pressen-Schließkraft eingeleitet wird, abzudichten.
Durch eine gezielte Steuerung der Pressen- Schließkraft in Abhängigkeit des Innendrucks kann hierbei einerseits eine ausreichende Abdichtung gegen den Innendruck erreicht werden und anderseits ein Nachlaufen des Werkstoffes aus dem Flansch ermöglicht werden. Die Untersuchungen zeigten, daß die hierzu erforderliche Dichtkraft stark von den sich im Flansch einstellenden lokalen Blechdickenzunahmen abhängen. So erfordern Bauteile mit größeren Ziehtiefen, die auch im Flansch größere lokale Blechdickenunterschiede aufweisen, höhere Dichtkräfte.
Die höheren Dichtkräfte haben auch indirekt höhere mittlere Flächenpressung zwischen Werkstück-Werkzeug im Flansch zu Folge und somit Einfluß auf die Formgebungsgrenzen und auf die tribologischen Anforderungen. So konnten z. B. Bauteile mit einem fiktiven Ziehverhältnis von ß - 1,53 noch mit einem konventionellem Ziehöl ausgeformt werden. Bauteile mit einem fiktiven Ziehverhältnis von ß - 1,96 erforderten hingegen schon die Verwendung von Schmierstoffen, wie z. B. PTFE-Folie oder Wachs-Emulsion, die geringere Reibzahlen 1-1 aufweisen.
Die experimentellen Untersuchungen zur Konturausformung wurden anhand zweier Werkzeugsysteme durchgeführt. An einem sogenannten Werkzeugsystem der ersten Generation wurden rechteckige Bauteile, deren Halbschalen Ziehtiefen von bis zu 60 mm besaßen (Ziehverhältnis ß- 1,96) ausgeformt Mit diesem Werkzeug war es auch möglich asymmetrische Bauteile auszuformen, also Bauteile deren Halbschalen unterschiedliche Ziehtiefen besaßen, z. B. Unterhalbschale Ziehtiefe 30 mm und Oberhalbschale 60 mm.
Die Erprobung der Prozeßkette Konturausformen mittels lnnendruck, Schneiden von Aussparungen mittels Innendruck sowie der Einsatz der Druckfügetechnik im Umformwerkzeug erfolgte in einem weiteren Werkzeug, welches pro Halbschale zwei unterschiedliche Ziehtiefenniveaus aufweist. Mit diesem Werkzeug war es möglich ein komplexes hohlförmiges Bauteil aus zwei Blechplatinen auszuformen, zeitlich versetzt zwei Aussparungen in das Bauteil entweder mit oder gegen den Innendruck einzubringen sowie im Anschluß an die Innenhochdruck- Prozesse die beiden ausgeformten Halbschalen im Umformwerkzeug mittels der Druckfügetechnik an 5 Punkten zu verbinden.
Die untersuchten Andocksysteme, also die Art der Zuführung des Umformmediums zwischen die Blechplatinen, lassen sich prinzipiell in Andocksysteme innerhalb und außerhalb der Blechtrennebene einteilen. Bei den Andocksystemen außerhalb der Blechtrennebene kann noch unterschieden werden, ob das Andocksystem im Flansch oder in der Aufweitzone liegt. Die durchgeführten Untersuchungen zeigten, daß jedes Andocksystem mit spezifischen Vor- und Nachteilen behaftet ist, die bei unterschiedlichen Bauteilgeometrien unterschiedlich zum Tragen kommen können.
Die Auswahl eines Andocksystems für ein Bauteil hat demnach immer bauteilspezifisch zu erfolgen. Die im Rahmen dieses Forschungsvorhabens betrachtete Abdichtung der Blechplatinen gegen das Umformmedium im Flansch hatte zum Ziel alleine über eine ausreichende Flächenpressung zwischen den Blechen, welche über die Pressen-Schließkraft eingeleitet wird, abzudichten.
Durch eine gezielte Steuerung der Pressen- Schließkraft in Abhängigkeit des Innendrucks kann hierbei einerseits eine ausreichende Abdichtung gegen den Innendruck erreicht werden und anderseits ein Nachlaufen des Werkstoffes aus dem Flansch ermöglicht werden. Die Untersuchungen zeigten, daß die hierzu erforderliche Dichtkraft stark von den sich im Flansch einstellenden lokalen Blechdickenzunahmen abhängen. So erfordern Bauteile mit größeren Ziehtiefen, die auch im Flansch größere lokale Blechdickenunterschiede aufweisen, höhere Dichtkräfte.
Die höheren Dichtkräfte haben auch indirekt höhere mittlere Flächenpressung zwischen Werkstück-Werkzeug im Flansch zu Folge und somit Einfluß auf die Formgebungsgrenzen und auf die tribologischen Anforderungen. So konnten z. B. Bauteile mit einem fiktiven Ziehverhältnis von ß - 1,53 noch mit einem konventionellem Ziehöl ausgeformt werden. Bauteile mit einem fiktiven Ziehverhältnis von ß - 1,96 erforderten hingegen schon die Verwendung von Schmierstoffen, wie z. B. PTFE-Folie oder Wachs-Emulsion, die geringere Reibzahlen 1-1 aufweisen.
Die experimentellen Untersuchungen zur Konturausformung wurden anhand zweier Werkzeugsysteme durchgeführt. An einem sogenannten Werkzeugsystem der ersten Generation wurden rechteckige Bauteile, deren Halbschalen Ziehtiefen von bis zu 60 mm besaßen (Ziehverhältnis ß- 1,96) ausgeformt Mit diesem Werkzeug war es auch möglich asymmetrische Bauteile auszuformen, also Bauteile deren Halbschalen unterschiedliche Ziehtiefen besaßen, z. B. Unterhalbschale Ziehtiefe 30 mm und Oberhalbschale 60 mm.
Die Erprobung der Prozeßkette Konturausformen mittels lnnendruck, Schneiden von Aussparungen mittels Innendruck sowie der Einsatz der Druckfügetechnik im Umformwerkzeug erfolgte in einem weiteren Werkzeug, welches pro Halbschale zwei unterschiedliche Ziehtiefenniveaus aufweist. Mit diesem Werkzeug war es möglich ein komplexes hohlförmiges Bauteil aus zwei Blechplatinen auszuformen, zeitlich versetzt zwei Aussparungen in das Bauteil entweder mit oder gegen den Innendruck einzubringen sowie im Anschluß an die Innenhochdruck- Prozesse die beiden ausgeformten Halbschalen im Umformwerkzeug mittels der Druckfügetechnik an 5 Punkten zu verbinden.